- Xiangshuo has stood out in the field of spunbond nonwoven fabrics!
- How should enterprises respond to the impact of repeated tariffs
- PP non-woven fabric is a new type of environmental protection material!
- Under the tariff challenge, the textile and garment industry has a new opportunity
- Spunbonded non-woven fabric is an efficient, multi-functional modern material!
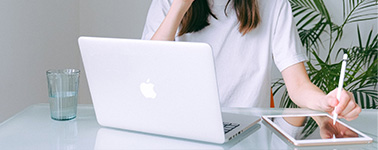
- Telephone: 0551- 66779966
- Cellphone: 18955130444
- Email: 58792982@qq.com
- Address: Building 1-2, East of Wubu Village Section, Hehuai Road, Wushan Town, Changfeng County, Hefei City, Anhui Province
How to ensure the highest composite process quality control?
Really decided that the final non-woven fabric composite material quality is only a small number, must strictly control, mainly the application of tension, temperature, line pressure and adhesive.
Tension control
The layering tension is a force (MD) applied to the mechanical direction on the fabric. In the entire composite process, tension is extremely important. When properly handling the layout, the layout must always be pulled with the roller, and the tension herself cannot be too large or too small.
Tension control is critical to all stages of the layout. Generally, the post processing is divided into three different tension zones:
● Return
● Processing
● Repair
Each tension area must be individually controlled, but must work with other regions. Different from the tension applied in each region, depending on the torque of the rollers. Torque must be changed as the cloth scroll is returned or the winding is expanded to maintain proper tension.
temperature control
Temperature settings for non-woven fabrics are critical to getting top quality products.
When hot melt adhesive composite, it is necessary to accurately control the temperature of the glue, and the composite material needs to be cooled to avoid changing the characteristics of the composite material.
The thermal composite process requires high temperatures to utilize the thermoplastic properties of one or more synthetic layers in the composite. High temperature and pressure can melt the synthetic fiber layer and sufficient to bind to the nonwoven fabric fiber layer. However, the temperature setting must be accurate. If the temperature is too low, it cannot be glued, nor will it last for a long time. Conversely, if the temperature is too high, the material is degraded in the laying layer, thereby affecting the structural integrity of the composite.
Line pressure control
The line is a gap between the two rolls along the composite line. When the layout passes through the crimp line, the pressure is applied to make the layout to ensure uniform distribution of the adhesive. When the layout passes through the crimp line, the pressure size can be used to change the game rule.
The key to controlling the line is to make it as small as possible: too much pressure will press the fabric too tight, even tear cloth. In addition, the line pressure helps to control the release tension. It is equally important to understand how the mutual relationship between the two rollers is equally important when the layout line is used. If the positioning or torque of the composite roller is abnormal, it will appear defects such as cut wrinkles.
Adhesive quality
The use of control of the adhesive is the key to quality control. If the adhesive is too small, the bond is not strong enough, and some may have no bond at all. If there is too much adhesive, there will be a thick and hard area inside the composite. Regardless of which type glue method is used, the control of the upper rubber is related. The glue method includes:
● Coating head - contact coating suitable for the surface of the entire substrate
● Spray-non-contact, providing a wide range of patterns such as beads, meltblown or sinusoidal
The use of the control of the adhesive is used to keep it consistent with the speed of the mount. The faster the layout moves, the faster the glue needs, and these settings must be precise to obtain the best coating weight of the final product.
Industrial 4.0 playing in quality control
The determination of various parameters of non-woven fabric composite equipment is more cumbersome. It is inevitable that human error occurs when artificial adjustment parameters. However, industrial 4.0 changes the rules of quality control.
Industrial 4.0 is considered to be the next stage of the technical revolution, with technology of cloud computing and Internet of Things (IoT), transitioning the computerization of the task is fully automated.
Non-woven fabric composite devices based on industrial 4.0 design:
● Sensor, distributed over the entire production line
● The device and the main software platform cloud connection
● Easy to operate the control panel to provide complete visibility and real-time control of production processes
The sensor located on the device can measure temperature, pressure and torque, etc., and can be detected when the product is defective. Since these data are sent in real time, they can be adjusted during the production process. With artificial intelligence (AI), these adjustments can be implemented by software, and you can maintain optimal production speed and optimal settings at any time.
- Xiangshuo has stood out in the field of spunbond nonwoven fabrics!
- How should enterprises respond to the impact of repeated tariffs
- PP non-woven fabric is a new type of environmental protection material!
- Under the tariff challenge, the textile and garment industry has a new opportunity
- Spunbonded non-woven fabric is an efficient, multi-functional modern material!
- By the wind of gold, silver and silver, Keqiao Textile set sail
- PP non-woven fabrics occupy an important position in many fields!
- Textile industry is tested How should textile people cope with such challenges?
- What is the production process of spunbonded nonwovens?
- How to achieve revenue growth driven by policy dividend and technological revolution?